Sandblasting
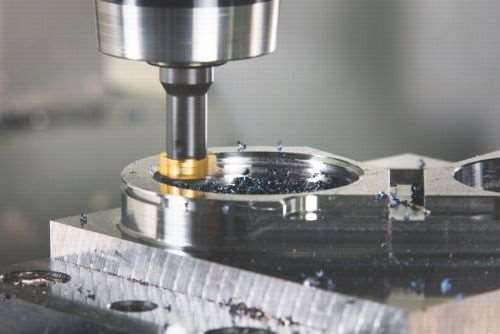
At present, sandblasting stands as a preeminent method for achieving top-tier cleaning of metals. This technique is instrumental in effectively eliminating a wide array of contaminants such as rust, bitumen, fuel oil, carbon deposits, and paint, amongst others, from surfaces.
How does it operate? The process is grounded in the interplay between abrasive particles and metal surfaces, necessitating the utilization of specialized equipment—a compressor designed to generate optimal pressure. The generated air stream captures and propels sand towards the targeted surface.
When compared to alternative cleaning methods, experts have discerned the following merits:
- Swift Cleaning: Sandblasting expedites the cleaning process due to its high-speed nature.
- Thorough Removal: It ensures thorough and efficient removal of all types of contaminants.
- Versatility: The market offers an extensive array of compressors, enabling selection of models tailored to specific parameters and dimensions.
- Availability of Components: A wide range of components and consumables are available for addressing diverse tasks.
- Superior Characteristics: In terms of effectiveness in eliminating contaminants, sandblasting equipment significantly outperforms liquid-based solutions.
Our team of experts is poised to assist you in choosing a compressor that takes into account every detail. Additionally, we offer custom sandblasting services:
- Optimal Work Conditions: The device's size and weight should provide a comfortable work environment.
- Safety Assurance: The manufacturer must ensure that the pressure vessel adheres to all safety standards.
- Performance Considerations: Excessive sleeves and fittings could impede performance.
- Sleeve Diameter: The sleeve diameter should not be less than 1 inch.
- Abrasive Compatibility: Ideally, the equipment should accommodate a broad range of abrasives, from sand to cast iron shot.
- Safety Enhancements: To enhance safety, a compressor with an automatic fuse mechanism can be considered.
- Pressure Vessel Maintenance: The pressure vessel warrants dedicated maintenance.
- Volume Requirements: The pressure tank should possess the requisite volume.
- Operation Duration: A fully loaded abrasive-laden device should operate for no less than half an hour.
- Dosing Mechanism: A dosing mechanism is advantageous for optimizing sand consumption.
- Inspection Hatch Size: A larger inspection hatch is preferable for convenience and efficiency.
In conclusion, sandblasting has emerged as a premier method for meticulous cleaning of metal surfaces, offering speed, efficiency, and adaptability across diverse applications.
+39 035 236452
sale@triestepg.com
Trieste Procurement Group SRL
Via Sant'Alessandro, 24122 Bergamo (BG)